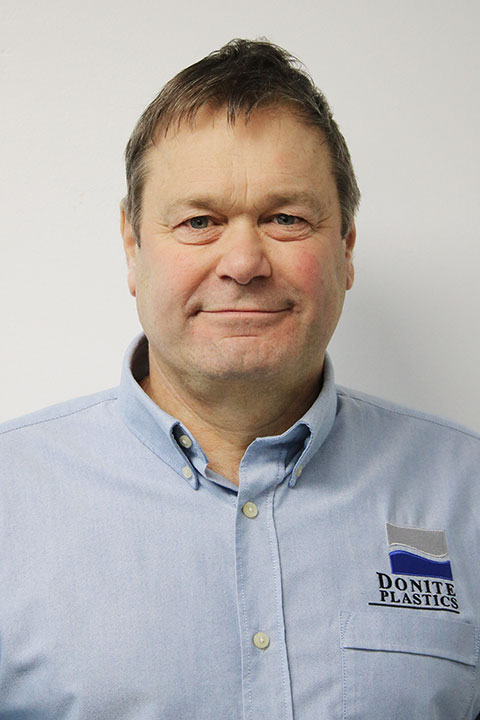
Michael Knight
Managing Director
Co-founder and Managing director of Donite Plastics. Michael is passionate about design and still gets involved with customers projects when time allows.
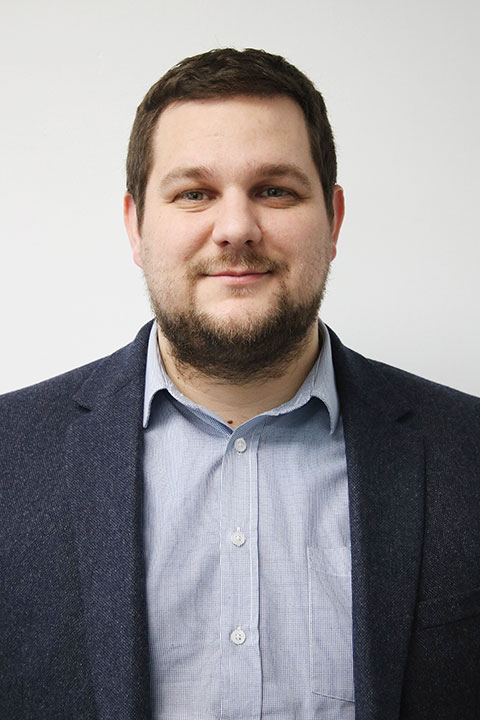
Stephen Kissick
Business Development Manager
With roots in engineering, Stephen focuses on development of the company, both internally with improvement initiatives and working with key clients to develop new business.
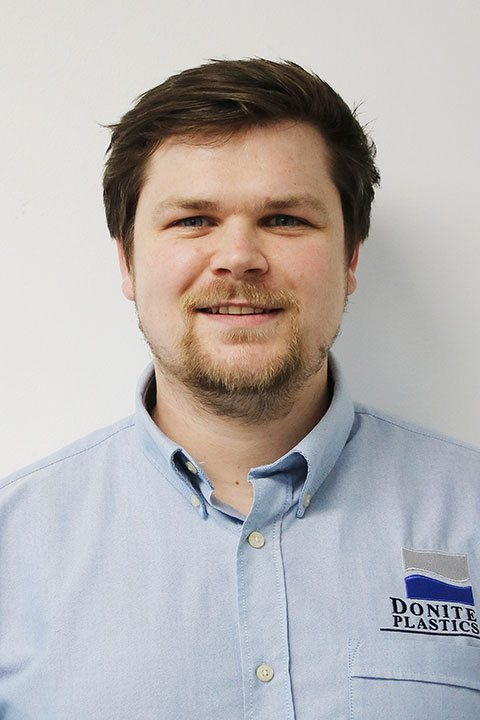
Patrick Knight
Engineering/R&D Manager
With background as a Development Engineer, Patrick has worked in a range of R & D projects and manufacturing efficiency. Quality comes naturally as the team works towards AS 9100.
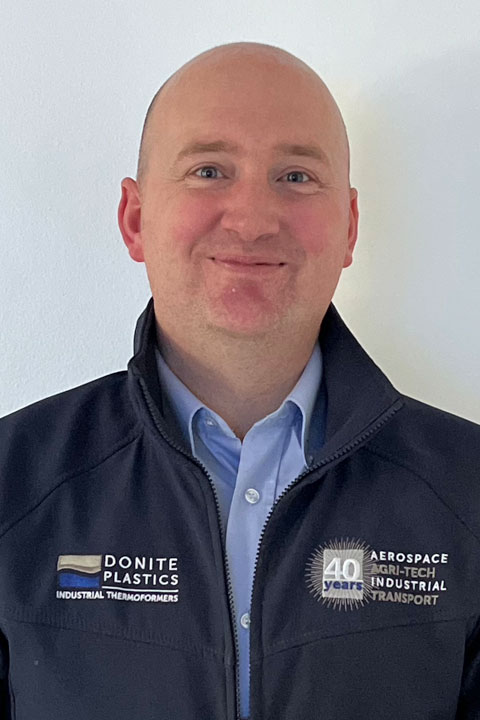
Diarmuid Grant
Operations and Supply Chain Manager
Holding a degree in Engineering Management, Diarmuid worked with Hovis Bakery for 13 years gaining experience as a Process Improvement Manager, Assistant Manager, Supply Chain Manager and Manufacturing Manager and brings strong leadership, relationship building and management skills.
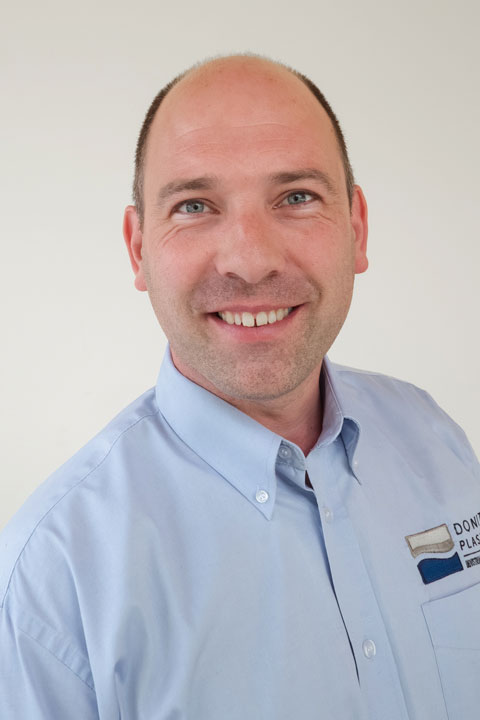
Matthew Revels
General Manager
Matthew joins the Saintfield-based company from Illig UK, bringing extensive engineering, project management and leadership experience to the role. He will oversee the strategic vision for Donite Plastics, in addition to new business, product development and day-to-day activities, as well as ensuring the company is at the forefront of the latest thermoforming technologies and smart factory systems.
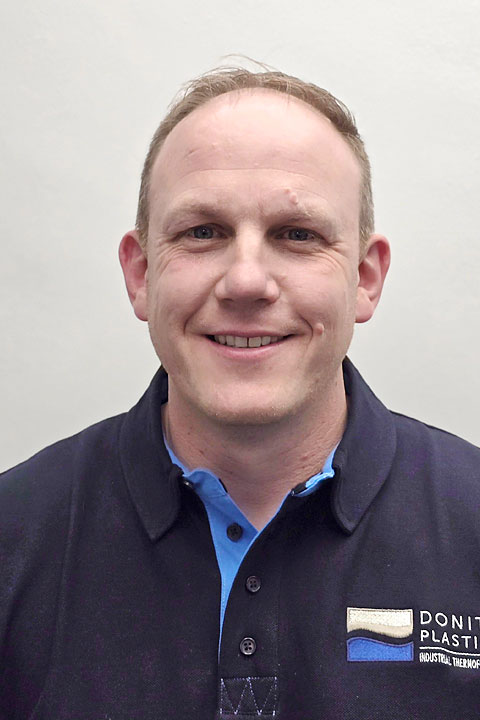
Alister Heatlie
New Product Development & Commercial Manager
Extensive experience in manufacturing, with a focus on design and New Product Development Introduction, and over seven years’ experience in the aerospace sector namely within main cabin interiors, Alister’s primary focus is implementing compliant new products through the manufacturing NPI gates.
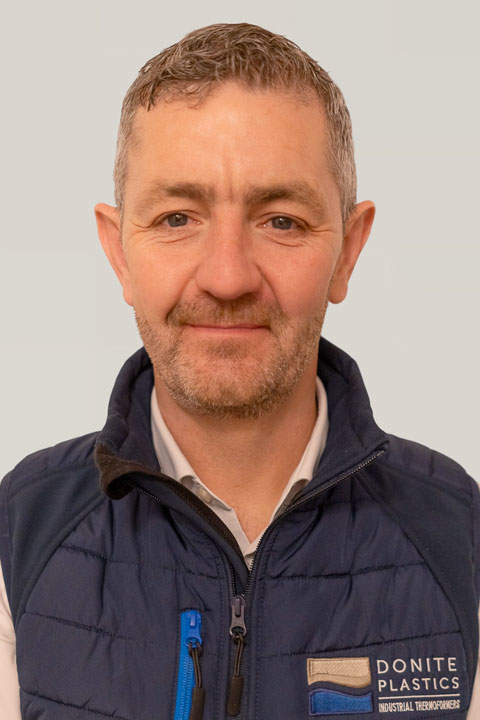
Robbie Marsh
Quality and Process Improvement Manager
With 25+ years of experience in quality management and manufacturing, Robbie specialises in lean methodologies, process optimisation, and team leadership. As our Quality and Process Improvement Manager, Robbie will enhance product quality, streamline production, and foster continuous improvement, reinforcing Donite's position as a leader in plastics manufacturing.
Quality
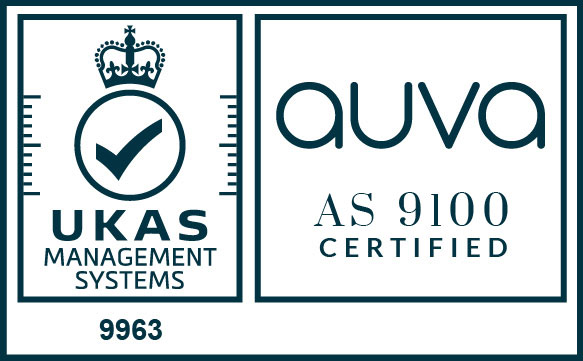
Donite Plastics commitment to quality is exemplified by its adherence to the AS9100 standard, which is specifically tailored for the aerospace industry. This standard builds on the ISO 9001 framework, adding additional requirements to address the unique needs of aviation, space, and defence sectors. By meeting these stringent requirements, Donite ensures that its thermoformed products are designed, manufactured, and assembled to the highest standards of quality and reliability.
This dedication to quality, involves rigorous quality control processes, continuous employee training, and a strong focus on customer satisfaction.
These efforts help Donite Plastics maintain its reputation for excellence in the aerospace industry.
Environment
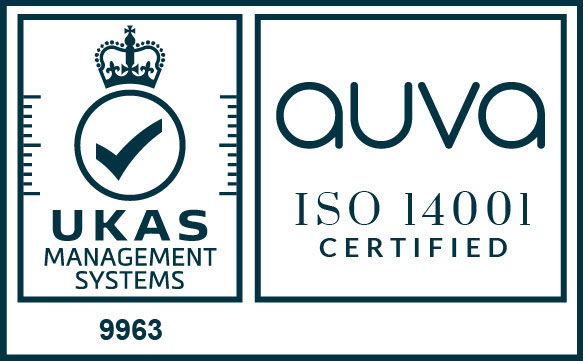
We aim to be a responsible and caring company, by reducing the carbon footprint of the products we make. Donite’s ethos is to supply a robust product with longevity; parts which can be reused time and time again. We are not a supplier of Single Use Plastics and ensure our offcuts and waste plastics are recycled. Reduction in the amount of waste going to landfill is vitally important. Donite specifies and uses material with recycled content when possible, and helps our customers to reduce their impact on the environment.
Experience and expertise with plastics
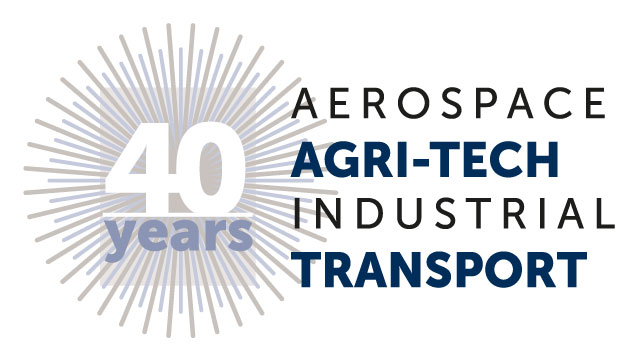
Donite Plastics specialize in the design and manufacture of custom moulded plastic parts using vacuum forming and other processes. These processes are ideal for large, medium or small batch quantities and even one-off prototypes. Donite is based about 5 miles south of Belfast - in Saintfield, County Down.
Donite prides itself in the comprehensive service that it offers. This includes full CAD/ CAM design and manufacturing facilities.
Facilities include full 5 axis machining and trimming as well as the large format Vacuum Forming. They have been an EN ISO 9001 quality assured company since 1997. Their processes and systems are continually being developed and improved and now boast 9100 and 14001.
Recycling
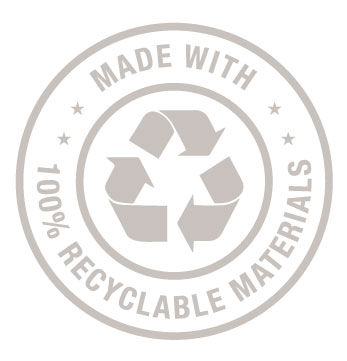
At Donite Plastics we are committed to sustainability by using 100% recyclable plastics whenever possible, with a renewed focus on reducing our carbon footprint. We endeavor to recycle 100% of offcuts and skeletal waste plastic back into the plastic streams.
Trade bodies
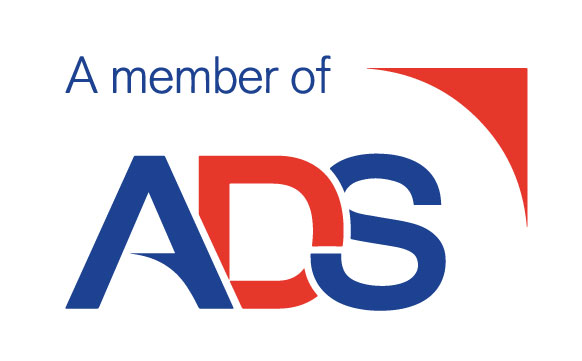
Donite are members of ADS, the UK trade body for Aerospace, Defence and Security. This gives us access to in-person events and expertise in specialist areas such as supply chain excellence, procurement and R&D funding. The support from ADS gives is insight and connections to make informed decisions re changes in the industry and remain competitive.
Donite Plastics has worked with some of the UK's leading manufacturing companies and has built strong relationships with them by continually striving to exceed their expectations.
Year | A brief history of Donite |
---|---|
1981 | Richard Donaldson and Michael Knight founded Donite Plastics, initially making motorcycle fairings and custom-moulded GRP parts. |
1990 | Donite became Northern Ireland’s first industrial vacuum forming service with the purchase of its first vacuum forming machine. |
1999 | Vacuum forming accounted for 87% of sales, overtaking GRP. |
2007 | Incorporated as Donite Plastics Ltd, with Michael Knight as sole director. |
2015 | Expanded services to include CNC machining, line bending, plastic punching/pressing, and laser cutting. |
2017 | Relocated to a new site in Saintfield, Co. Down, with extensive development opportunities. |
2018 | Installed large vacuum forming and 5-axis CNC machines, enhancing industry competitiveness. |
2023 | Planning approved for a new factory extension and development of a 2.5-acre site. |
2024 | Achieved AS9100 and ISO 14001 certification and received the largest CMS automated loading vacuum former in the UK and Ireland. |